
Comportement et étude des graves-émulsion
Bilan de la coopération public-privé : acquis et suites à donner
La synthèse présentée dans cet article repose largement sur les travaux du groupe de travail dédié à la coopération. Il tient également compte des enseignements tirés d'autres réalisations, dont les essais sur le manège Ifsttar, les recherches initiées par l'Usirf (désormais Routes de France) et, d'une manière générale, les retours d'expérience des divers acteurs de la construction routière.
Les enrobés à l’émulsion de bitume en général, et les graves-émulsion (GE) en particulier, présentent de grands avantages économiques et environnementaux. Pourtant, l’usage des GE a longtemps été cantonné aux opérations de reprofilage- rechargement. Un développement significatif de cette technique ne peut venir que de son extension aux apports de structure dans les chaussées.
Cependant, leur formulation, leur évaluation et leur dimensionnement relevaient, encore récemment, de démarches empiriques, généralement issues de compétences locales. Pour caractériser les performances spécifiques de ces matériaux et aboutir à des méthodologies d’étude et de dimensionnement, il est apparu nécessaire de suivre leur évolution in situ et d’évaluer parallèlement leur comportement en laboratoire (figure 1).
figure_1.jpg
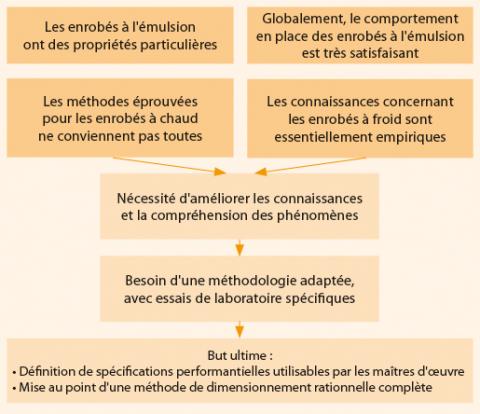
L’objectif est d’amener ainsi la connaissance des matériaux routiers traités à l’émulsion à un niveau équivalent à celui des enrobés à chaud ou des matériaux hydrauliques et de développer leur utilisation sur le terrain.
Contexte
Deux importantes expérimentations ont été menées par deux entreprises majeures sur le manège de fatigue du LCPC (maintenant Ifsttar) de Nantes, l’une en 1993-1994, l’autre en 19991-2.
Elles avaient montré, entre autres, la bonne tenue d’enrobés à l’émulsion sous un grand nombre de chargements et mis en évidence certaines particularités de leur comportement. En 1997, la direction des Routes et l’Usirf ont conduit une évaluation des graves-émulsion structurantes (GES) basée sur l’étude et la réalisation d’une section de référence, dont le suivi n’a été poursuivi que sur deux ans. Ce projet a fourni des premières informations quant à la pertinence – ou non – de divers essais de laboratoire3.
Plus tard, à la suite d’importantes recherches menées individuellement, les entreprises de l’Usirf ont mené un projet commun qui s’est appuyé sur la réalisation en parallèle du suivi en place de sections routières et de l’évaluation en laboratoire des performances des matériaux utilisés.
Trois sections de GE ont été construites en 2004 et suivies pendant 5 ans. Elles sont situées respectivement sur la RD 437 dans le Jura, la RD 10 en Corrèze et la RD 79 en Dordogne. Selon la même approche, trois sections de béton bitumineux à l’émulsion (BBE) ont été mises en oeuvre en 2005 et suivies pendant 5 ans4-7.
De son côté, l’Ifsttar, en liaison avec le Réseau scientifique et technique du ministère (RST, désormais Cerema) a démarré en 2006 l’opération OPTIMIRR (Optimisation des matériaux routiers économes et incorporant des recyclés de la route). Le premier thème de cette opération concernait les matériaux à l’émulsion. Il visait à poursuivre la veille technologique sur ces produits et à étudier leur comportement dans le temps. Ce programme incluait la réalisation de chantiers-témoins instrumentés, suivis dans le long terme, et l’examen des méthodes d’essai en laboratoire pertinentes.
Genèse de la coopération public-privé
Ayant constaté, lors de divers contacts, qu’ils se posaient les mêmes questions et poursuivaient les mêmes objectifs, l’Ifsttar, associé au RST, et l’Usirf ont décidé d’unir leurs efforts dans une recherche commune consacrée aux GE (figure 2).
figure_2.jpg
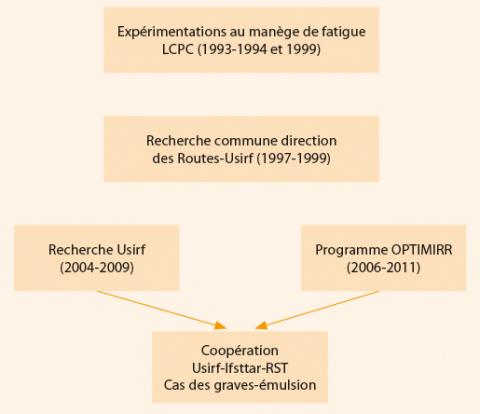
Les chantiers expérimentaux
Trois sections de GE ont été étudiées, construites et suivies. Elles ont été choisies pour représenter à la fois des climats et des granulats différents. Ces chantiers sont les suivants :
- RD 20 (Haute-Garonne) : étés chauds, hivers doux – granulats alluvionnaires de Garonne semi-concassés – émulsion « d’arrière- saison » à base de bitume 160/220 fortement fluxé – construite en octobre 2006 – trafic T2 (photo 1) ;
photo_1_rd_20_haute-garonne.jpg
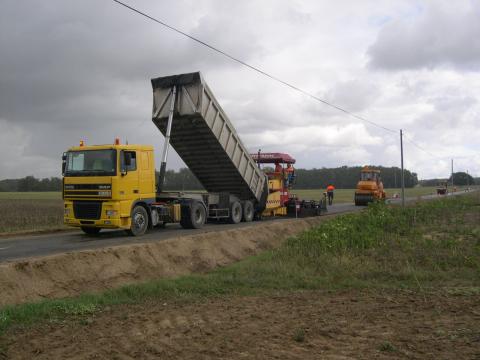
- RD 44 (Ille-et-Vilaine) : climat océanique (humide et doux) – granulats de roche massive dure (cornéenne) – émulsion de bitume 70/100 légèrement fluxé – construite en juillet 2008 – trafic T3 (photos 2) ;
photo_2_.png
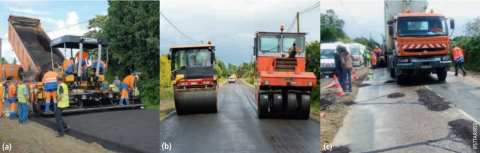
- RD 26 (Haute-Loire) : climat montagnard (altitude 1 200 m, hivers rudes, enneigés et ventés) – granulats de roche massive (basalte) – émulsion de bitume 160/220 non fluxé – construite en juin 2011 – trafic T4 (photo 3).
photo_3_.jpg
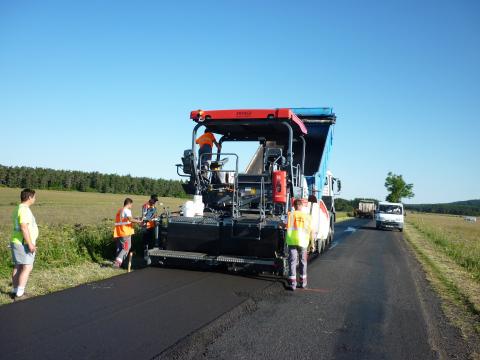
En outre, un complément de suivi a été effectué sur le chantier expérimental de la RN 126 près de Toulouse, construit en juin 1997, dans le cadre de la collaboration avec la direction des Routes, avec des granulats alluvionnaires de Garonne et une émulsion de bitume 70/100 non fluxé, supportant un trafic T2 (photo 4).
photo_4_.jpg
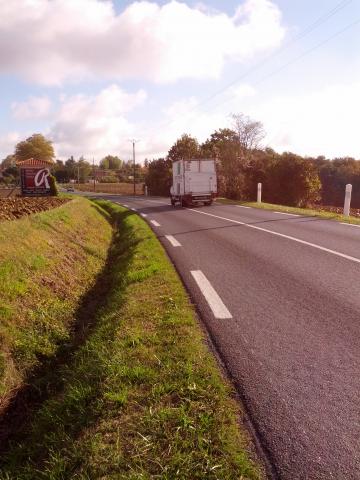
Les résultats acquis lors du suivi de la RD 20 et des études menées parallèlement en laboratoire ont été exposés dans des rapports internes Ifsttar/RST pour la RD 20.
Les résultats complets concernant la RD 44 ont été détaillés dans une série de 12 articles parus de septembre 2011 à juin 2012 dans la RGRA8-19.
Les enseignements tirés du chantier de la RD 26 ont été synthétisés dans un rapport du Conseil général de Haute-Loire – Cerema – Ifsttar – Usirf d’avril 2017. Ils font l’objet des deux articles dans le présent numéro de la RGRA.
Bilan de comportement
Excellent comportement global
À fin 2017, le suivi visuel des différentes sections s’est étendu sur des durées très significatives :
- 6 ans sur la RD 26 en Haute-Loire, construite en 2011 ;
- 9 ans sur la RD 44 en Ille-et-Vilaine, construite en 2008 ;
- 11 ans sur la RD 20 en Haute-Garonne, construite en 2006 ;
- 20 ans sur la RN 126 en Haute-Garonne, construite en 1997.
Il faut noter, de plus, qu’une bonne partie des GE concernées a été laissée sans revêtement (contrairement à la pratique normale) afin de mieux observer leur tenue sous trafic. Ainsi, les GE des RD 26 et 44 n’ont, à ce jour, pas été revêtues. Celle de la RD 20 est restée exposée pendant 8 ans. La majeure partie de la section de la RN 126 a été recouverte avec un enrobé coulé à froid (ECF) un an après sa construction ; le reste n’a reçu un revêtement qu’au bout de 18 ans (un enduit superficiel monocouche a été appliqué en 2005 sur la totalité de la section).
L’ensemble des observations visuelles témoigne d’un comportement globalement satisfaisant, avec absence de dégradation structurelle et bonne tenue de surface.
Tenue de surface
Les zones non revêtues n’ont pas montré de phénomène de plumage, ni de glaçage. La macrotexture apparaît convenable. Cela est remarquable pour les RD 20 et RN 126, soumises à des trafics lourds (classe T2) et dont la largeur n’est que de 6 mètres.
Pour l’ensemble, il faut toutefois noter qu’existent ponctuellement des zones de dégradation, dont l’aspect visuel est médiocre, mais qui tiennent correctement.
Tenue mécanique
Déformations permanentes
Aucun signe d’orniérage n’a été observé. Si cela ne prouve rien sous très faible trafic (RD 26), cette constatation est tout à fait significative pour les sections des RD 20 et RN 126, où le trafic est élevé et canalisé (faible largeur des bandes de roulement). Ce comportement est d’autant plus remarquable que les GE y sont constituées avec des granulats semi-concassés d’origine alluvionnaire comprenant des faces arrondies et polies.
Pour mémoire, les expériences menées sur le manège de l’Ifsttar avaient montré que les déformations du profil transversal (sous 1 million de passages de jumelages de 6,5 tonnes) provenaient du tassement, surtout des couches sous-jacentes et pas d’un fluage de la GE.
Fissuration
Aucun faïençage pouvant évoquer de la fatigue n’a été relevé. Sur la RN 126, une fissuration à maillage large est apparue à 7 ans sur la partie non revêtue, sans déformations. Cette fissuration a peu évolué dans le temps.
Le seul type de dégradation affectant l’ensemble des GE est une fissuration localisée en rive, correspondant à la fois à une sous-épaisseur mise en oeuvre et à un manque d’épaulement latéral (accotements de qualité médiocre et entrées d’eau dans le bord de la GE). Ailleurs, c’est-à-dire sur la majeure partie de chacun des chantiers, la GE a conservé son intégrité (absence de fissuration).
Apport structurel
Les mesures de déflexion et de rayon de courbure (figures 3 et 4), qu’elles soient effectuées au déflectographe ou au déflectomètre à masse tombante (Falling Weight Deflectometer (FWD)) ont permis de quantifier l’apport structurel d’une couche de graves-émulsion structurantes (GES). Cette capacité de renforcement est très significative, surtout si on la rapproche des niveaux de rigidité modestes mesurés sur les différentes GE.
figure_3.jpg

figure_4.jpg
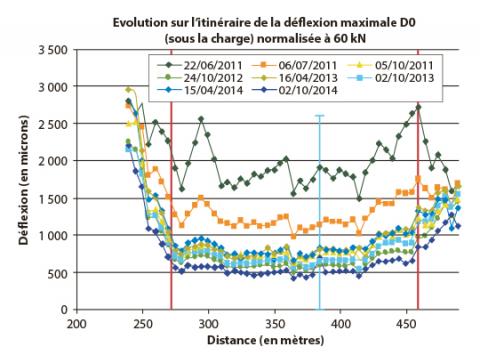
De plus, ces mesures ont confirmé le caractère évolutif des GE dans le temps : la diminution des déflexions traduit l’augmentation de leur module de rigidité accompagnant leur consolidation et le durcissement du liant. Ce phénomène est marqué surtout lors des deux premiers étés en place.
Parallèlement aux mesures en oeuvre, les essais menés en laboratoire sur des échantillons prélevés dans la couche de GE à différents âges ont quantifié précisément l’évolution du liant (figures 5, 6 et 7). Celle-ci est notable, mais il faut remarquer que, malgré ce durcissement, les GE ont continué d’avoir un comportement de matériau souple, qui se manifeste par une bonne capacité de déformation sous charge (modules de rigidité relativement bas) et une capacité d’autoréparation avérée.
figure_5.jpg

figure_6.jpg
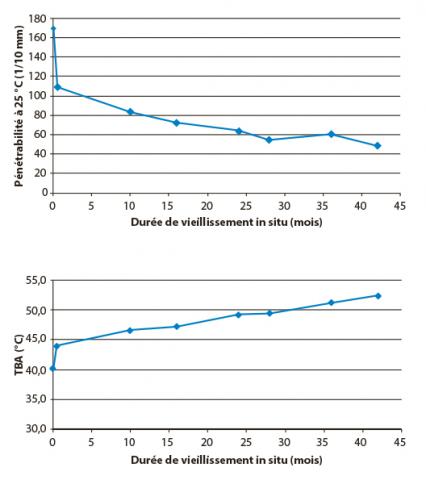
figure_7.jpg
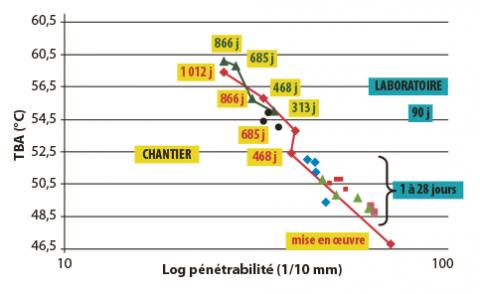
Perméabilités
Afin de répondre aux inquiétudes que certains pourraient avoir au vu des valeurs élevées des pourcentages de vides mesurés sur les GE, des essais de perméabilité ont été réalisés par Eurovia sur des éprouvettes de la GE de la RD 26. Il convient de rappeler ici que les vides mesurés, au banc gamma ou par méthode hydrostatique, sont des vides apparents, qu’ils soient communicants ou non.
Rappelons que des recherches, menées par ailleurs, ont montré que, dans les enrobés à l’émulsion, une part importante des vides sont de très petite taille, contrairement aux enrobés à chaud4.
Deux protocoles d’essai de perméabilité ont été suivis : mesure sous charge constante verticale (norme NF EN 12697-1920) (photo 5) et mesure des vides communicants (norme NF P98-254-221) (photo 6).
photo_5.jpg
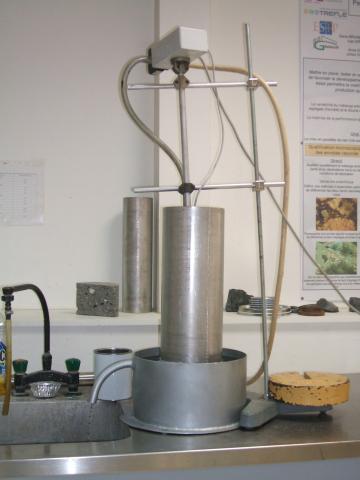
photo_6.jpg
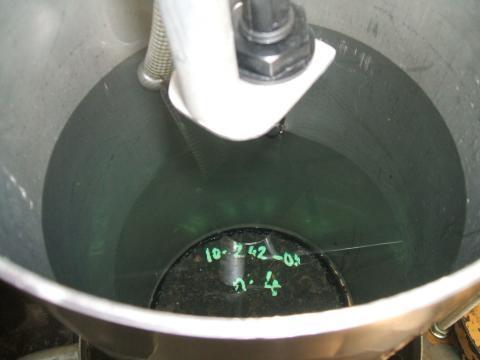
Le coefficient de perméabilité verticale Kv sur éprouvettes carottées sur chantier est de 3,9.E-6 m/s à 10 mois et de 3,7.E-6 à 16 mois pour une teneur en vides de 15 %, ce qui dénote une très faible perméabilité.
La détermination des vides communicants donne 0,1 à 0,4 % sur éprouvettes moulées en laboratoire à des teneurs en vides de 15,7 à 21,4 %. Le même essai pratiqué sur carottes extraites du chantier démontre que l’eau ne passe pas à travers les corps d’épreuve.
Ces résultats sont tout à fait rassurants quant à la capacité de la GE à constituer une barrière efficace vis-à-vis des entrées d’eau dans la chaussée.
Méthodologie d’étude
Les grandes lignes de la méthodologie d’étude des GE ont été ébauchées dès le début des années 200022. Ses différentes étapes ont été testées au cours des opérations de recherche menées dans le cadre des chantiers expérimentaux décrits plus haut.
En fait, cette méthode s’applique à tous les enrobés à l’émulsion fabriqués en centrale : GE et bétons bitumineux à l’émulsion (BBE).
La méthode d’étude proposée n’inclut pas la formulation de l’émulsion elle-même, qui correspond avant tout à un savoir-faire de fabricant. Elle comprend globalement quatre phases : constitution du mélange, essais sur mélange frais, mûrissement accéléré, essai sur mélange mûri.
Phase préalable (nouveau mélange)
La mise au point d’un nouvel enrobé à l’émulsion commence par la sélection de ses constituants. Généralement, la raison économique conduit à retenir a priori les granulats disponibles localement, pourvu qu’ils soient conformes en termes de caractéristiques intrinsèques et de coupures granulaires.
Le formulateur choisit ensuite une émulsion d’enrobage, selon son expérience et la disponibilité des produits.
Le technicien de laboratoire procède alors à des essais de mélange dits « en gamelle » (méthode LPC n° 7423), qui renseignent empiriquement sur la qualité (ou la difficulté) d’enrobage, la vitesse de rupture, la maniabilité, l’essorage, l’éventuelle tendance au désenrobage mécanique. Si nécessaire, la formulation de l’émulsion est modifiée (teneur en bitume, nature et dosage de l’émulsif, pH, fluxant éventuel). Simultanément, le dosage en eau d’apport est ajusté.
Essais sur mélange frais
Fabrication en laboratoire
Tous fonctionnent en discontinu. Il n’est donc pas possible de reproduire exactement en laboratoire le fonctionnement des malaxeurs des centrales à froid, qui sont pratiquement tous continus.Les malaxeurs existant dans les laboratoires sont de types variés, que l’on peut regrouper en deux grandes catégories : ceux à un axe vertical et ceux à deux arbres horizontaux (photo 7).
photo_7.jpg
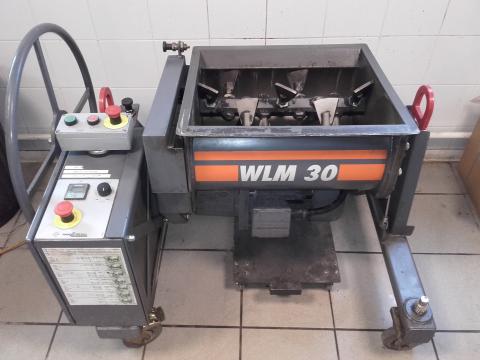
Néanmoins, quel que soit le modèle de malaxeur, il est essentiel que la fabrication en laboratoire suive le plus fidèlement possible la procédure prévue pour le chantier : ordre d’introduction des constituants, enrobage simple ou séquencé, répartition de l’eau et de l’émulsion à tel ou tel stade du malaxage, préenrobage éventuel de telle ou telle fraction granulaire…). Ces dispositions sont fondamentales pour garantir que le mélange de laboratoire soit représentatif du matériau qui sera mis sur la route.
Un autre paramètre important est la température du mélange au moment de son malaxage. En règle générale, pour un enrobé « à froid », on opère à la température ambiante du laboratoire (normalement entre 18 et 25 °C).
L’expérience a montré que des températures anormalement basses ou hautes sont susceptibles de fausser les résultats obtenus en laboratoire. Il est donc préconisé de respecter la fourchette de températures ci-dessus, sauf indication spécifique différente. Ainsi, s’il est prévu d’employer un procédé « semi-froid » selon lequel le mélange est fabriqué au-dessus de l’ambiante (et en-dessous de 100 °C), sa préparation en laboratoire doit répliquer le mieux possible le procédé prévu pour le chantier.
Qualité d’enrobage – Sensibilité au désenrobage
Sur chantier, la qualité d’enrobage peut varier considérablement d’un matériau à l’autre. Pour évaluer et comparer objectivement, il faut la quantifier par le pourcentage de surface minérale couverte par le liant bitumineux. La méthode idéale est l’analyse d’image, sur le matériau ou sur photo numérique. Le plus souvent, on se contente de l’observation visuelle.
Le tableau 1 indique l’échelle de notation telle que définie dans la norme NF P98-257-124.
tab_1.jpg
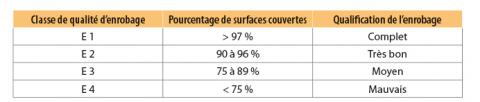
Un enrobage imparfait est acceptable pour les matériaux d’assise. En revanche, pour les enrobés de surface, un enrobage incomplet entraîne une sensibilité à l’eau et surtout le risque de plumage sous trafic.
Les observations sur chantier montrent que certains enrobés à l’émulsion se désenrobent ensuite partiellement au cours des diverses manutentions qu’ils subissent, ce phénomène affectant surtout les gros éléments.
Si l’on craint cette tendance au désenrobage, il convient de soumettre le matériau frais à des sollicitations pouvant le désenrober. Diverses possibilités existent, la plus simple consistant à prolonger le malaxage bien après obtention de l’enrobage maximum. On peut aussi laisser l’enrobé reposer 24 heures et réévaluer ensuite la qualité d’enrobage. Pour le désenrobage par l’eau, la démarche est analogue : l’enrobé frais est soumis à une immersion ou à un arrosage. Le cas est toutefois rarissime, les tensio-actifs classiquement utilisés étant des promoteurs d’adhésivité.
Égouttage
L’objectif de l’essai d’égouttage (méthode LPC n° 7525) est d’évaluer la quantité d’eau susceptible de s’égoutter du matériau entre sa fabrication et sa mise en œuvre. Il consiste à peser la quantité d’eau pouvant s’écouler du matériau enrobé placé sur un plan incliné, simulant une aire de stockage ou la benne d’un camion, pendant 24 heures. L’angle d’inclinaison est de 7° (+ ou - 2°). L’essai s’effectue soit en laboratoire, à température ambiante, soit à côté de la centrale de fabrication.
Les résultats peuvent conduire à adapter la formulation, essentiellement au niveau de la teneur en eau, qu’elle provienne d’ajout direct ou de pré-humidification de constituants. Ils peuvent aussi influencer l’organisation du transport du matériau entre la centrale et l’application.
Maniabilité – Montée en cohésion
À la différence des BBE, les GE n’ont jusqu’à présent jamais donné lieu à des problèmes de maniabilité, ce qui s’explique par leur plus faible teneur en liant. Néanmoins, dans certains cas particuliers, il peut s’avérer nécessaire de se préoccuper de cet aspect de leur comportement :
- pour les GE enrichies, dont la teneur en liant est intermédiaire entre celle des GE classiques et celle des BBE ;
- pour les GE que l’on souhaite stocker un certain temps avant mise en oeuvre, cas assez peu courant.
L’aptitude à la mise en œuvre d’un enrobé à l’émulsion (écoulement du matériau depuis la benne du camion, passage sous la table du finisseur) dépend fortement de la progression de rupture de l’émulsion et peut être évaluée à l’aide du maniabilimètre Nynas (méthode LPC n° 7626) (photo 8).
photo_8.jpg
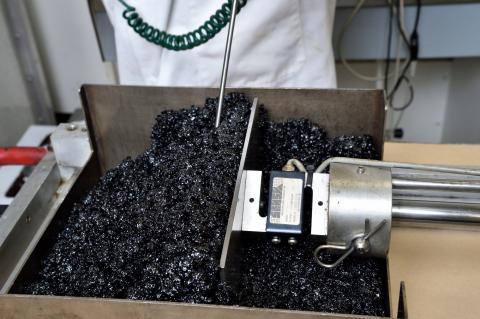
Eiffage a développé un moule de maniabilité Nynas demi-grandeur qui permet des mesures sur chantier, avec suivi de l’évolution du matériau lors de son transport entre la centrale et l’application sur la route.
La maniabilité est caractérisée par la force maximale nécessaire pour pousser une masse donnée de matériau foisonné. Elle peut être mesurée soit immédiatement après fabrication, soit après des temps de repos (« reprise ») croissants. Avec le second protocole, la vitesse de montée en cohésion peut être appréhendée.
Comme pour la fabrication, on opère généralement à la température ambiante du laboratoire, parfois à une température fixée en fonction des conditions locales du chantier ou du procédé spécial de fabrication choisi.
Si la force nécessaire dépasse un certain seuil, il convient soit de reformuler le matériau, soit d’organiser la mise en oeuvre pour en réduire les délais. Actuellement, il n’y a pas de valeur-limite universellement admise, mais on peut considérer que, pour une GE, à partir d’une force de 500 N environ, il faut se poser la question de la maniabilité.
Une autre méthode (LPC n° 76) consiste à mesurer le couple nécessaire à la décohésion du matériau à l’aide d’une « pale-ancre » fixée à un moteur d’entraînement équipé d’un capteur de mesure de couple (photo 9).
photo_9.jpg
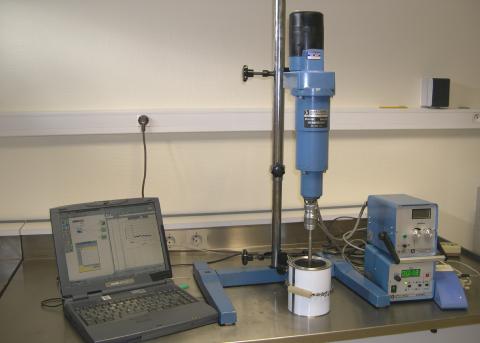
Les essais peuvent être pratiqués sur un matériau fraîchement fabriqué ou après conservation dans une enceinte climatique régulée en température et hygrométrie. Des tests réalisés après différents temps de conservation évaluent la vitesse de montée en cohésion. En pratique, ces données sont utiles pour l’optimisation des opérations de transport et de mise en œuvre sur chantier.
Cette méthode présente l’avantage de nécessiter des quantités de matériau nettement moindres que la précédente. Le conditionnement des échantillons à différents stades d’évolution est plus rapide et la suivi de la montée en cohésion en est facilité.
Compactabilité
L’aptitude au compactage des enrobés à l’émulsion s’évalue à l’aide de presses à cisaillement giratoire (PCG) (photo 10).
photo_10.jpg
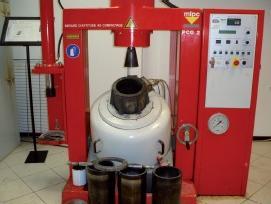
Les laboratoires disposent d’équipements divers :
- Des modèles MLPC PCG 2, qui ne sont plus fabriqués, sont encore en usage ici et là.
- La PCG 3, toujours fabriquée, est largement employée.
- D’autres types de PCG provenant de l’étranger sont apparues au cours des dernières années.
Cette diversité pose bien entendu la question de l’étalonnage des différentes machines les unes par rapport aux autres.
Il est intéressant de signaler l’existence d’un équipement pouvant être installé sur les PCG 3, qui recueille l’eau exsudée au cours de la densification et la pèse. Il est ainsi possible de suivre avec précision les phases du compactage : élimination de l’air, début et fin de l’exsudation d’eau, serrage du squelette minéral.
Les nombreux résultats de compactage de GE à la PCG montrent que ce type d’essai est discriminant quand il s’agit de comparer l’aptitude au compactage de différentes formulations. On peut donc se fonder dessus, soit pour optimiser une formulation, soit pour comparer les performances potentielles de deux mélanges.
En revanche, les essais à la PCG ne sont pas un outil intrinsèque de prédiction de compacités in situ, ces dernières dépendant largement des caractéristiques du support sur lequel la GE est posée. Les conditions météorologiques lors du chantier peuvent aussi influer dans une certaine mesure.
Mûrissement accéléré
Cette étape est fondamentale pour la méthodologie d’étude : il s’agit là de reproduire le passage de l’état frais, peu cohésif, à un état mûri correspondant à celui que le matériau atteindra à moyen terme, avec une cohésion notable.
Des recherches antérieures ont montré qu’il faut combiner chauffage et séchage pour provoquer une évolution suffisante. Elles ont prouvé qu’il n’y a aucun mûrissement significatif en dessous de 10 °C. Il est évidemment tentant d’opérer à une température élevée pour raccourcir le délai de mûrissement ; certains ont proposé 50, voire 60 °C. D’abord, un tel niveau de température risque, dans certains cas, de faire fondre le film de liant, perturbant ainsi la structure du mastic d’enrobage et modifiant la structure interne du matériau. En outre, les séquences de mûrissement à 50 ou 60 °C testées ont provoqué la fissuration des corps d’épreuve par séchage/retrait trop rapide. Au final, il a été décidé de faire mûrir à 35 °C, température réaliste pour une majorité de régions françaises.
Un autre facteur primordial pour le mûrissement accéléré est l’application d’une humidité relative basse, ce qui implique de disposer d’un débit d’air sec suffisant vis-à-vis du volume d’eau à extraire des éprouvettes placées dans l’enceinte. Au regard des possibilités des équipements, il a été décidé de viser une humidité relative (HR) de 20 %. On rappelle que le vent a, sur les chantiers, un effet de séchage et d’oxydation au moins égal à celui de la chaleur.
Les retours d’expérience à la suite des études menées en parallèle sur échantillons prélevés en place et sur éprouvettes fabriquées en laboratoire ont démontré que :
- Pour obtenir en laboratoire un état proche de celui atteint in situ après 2 ou 3 étés, le protocole de mûrissement ( 35 °C, 20 % HR) doit être appliqué pendant : 14 jours pour des « petites » éprouvettes (petite PCG, Duriez normal) ; 21 jours pour des éprouvettes « moyennes » (PCG 2 ou 3, Duriez dilaté) ; 21 ou 28 jours, selon la porosité du matériau, pour les plaques d’orniérage ; plus de 28 jours pour les grosses plaques dans lesquelles divers corps d’épreuve seront extraits par sciage ou carottage. Le prélèvement et surtout le mûrissement de grosses plaques (pour module ou fatigue) s’avère très difficile. Il est donc recommandé de leurs préférer le prélèvement d’échantillons ou la confection d’éprouvettes de petites ou moyennes dimensions.
- Le volume de l’éprouvette n’est pas le seul paramètre influent : il faut aussi prendre en compte le rapport entre la surface extérieure (S) et le volume (V) : S/V.
Le terme « proche » signifie qu’il n’y a pas de correspondance absolue. En effet, les conditions météorologiques (température, hygrométrie, pluviométrie... et vent !) peuvent être très variables dans le temps et dans l’espace, alors que les conditions de mûrissement sont rigoureusement maîtrisées au laboratoire.
Le mûrissement type Duriez classique (14 jours, 18 °C, 50 % HR) fait très peu évoluer l’enrobé. On peut considérer qu’il correspond à l’état « frais », atteint en place après quelques jours ou semaines faisant suite à la mise en œuvre (selon la météorologie).
Essais sur mélange mûri
Compression simple et tenue à l’eau (essai Duriez)
Les résultats confirment la pertinence de la procédure dite « Duriez aménagé » (photo 11). La compacité des éprouvettes moulées selon ce protocole (pression égale au tiers du « Duriez standard ») est du même ordre de grandeur que celle constatée in situ à la fin du compactage quand la GE est appliquée sur un support dont la portance est correcte. Le niveau de compacité correspond aussi au début de l’extrusion de l’eau lors d’essais à la PCG.
photo_11.png
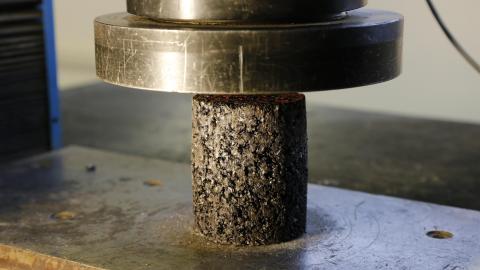
Les observations, mûrissement et écrasements d’éprouvettes Duriez se sont avérés produire des informations pertinentes en termes de compacités, durcissement du liant et tenue à l’eau.
Outre le mûrissement Duriez classique, il est utile de pratiquer aussi le mûrissement accéléré (14 jours, 35 °C, 20 % HR) des éprouvettes « Duriez aménagé », qui durcit sensiblement le liant, l’amenant à un état voisin de celui observé en place après 2 (ou 3) étés. En outre, ce mûrissement accéléré augmente sensiblement la tenue à l’eau des GE. Rappelons que la sensibilité à l’eau est traduite par le rapport immersion-compression r/R (r = résistance après immersion, R = résistance à sec).
La comparaison des rapports entre l’état frais et l’état mûri permet de quantifier le gain en tenue à l’eau amené par le mûrissement :
Résistance à l’orniérage
En laboratoire, la confection de plaques ayant des caractéristiques proches de celles obtenues in situ se heurte à deux difficultés :
- atteindre une compacité suffisante dans le moule ;
- parvenir à un mûrissement suffisant de la plaque, qui est enfermée dans le moule et peu exposée à l’air (photo 12).
photo_12.jpg

En raison de ces difficultés, les essais à l’orniéreur ont souvent été réalisés sur des plaques peu compactes et peu mûries. Malgré cela, la tenue à l’orniéreur s’avère très bonne. Cette performance s’explique par le caractère très frottant du squelette minéral des GE. D’une manière générale, les résultats d’essais à l’orniéreur s’avèrent pessimistes par rapport à la réalité observée en place. Un exemple marquant est celui de la RD 20, où aucun orniérage n’a été enregistré sous trafic lourd (T2), alors que l’essai à l’orniéreur avait été plutôt inquiétant. Rappelons que, sur cette section, la GE était formulée avec des granulats alluvionnaires et un bitume mou fortement fluxé.
Module de rigidité
Ce paramètre est apparu le plus à même de rendre compte de l’évolution du matériau dans le temps et d’établir le parallèle entre le chantier et le laboratoire. En effet, le module peut être mesuré sur des échantillons intacts prélevés dans la chaussée et des éprouvettes du même mélange fabriquées en laboratoire.
Il existe différentes méthodes de mesure du module. Les deux plus usitées sont, selon la norme de référence NF EN 12697-2627 :
- le module complexe sinusoïdal en flexion 2 points sur éprouvettes trapézoïdales (méthode 2 PB-TR) ou prismatiques (2 PB-PR) ;
- le module en traction indirecte sur éprouvettes cylindriques (IT-CY) (photo 13).
photo_13.jpg

La seconde s’avère très commode, car elle ne nécessite qu’un volume limité de matériau, est rapide d’exécution et permet d’opérer directement sur un échantillon de couche mince.
Moins souvent, d’autres protocoles ont été utilisés :
- le module en traction directe sur éprouvette cylindrique (DT-CY) ou prismatiques (DT-PR) ;
- le module complexe en compression uniaxiale sur éprouvettes cylindriques selon la norme AASHTO TP 62 07 (MC-CU).
Le résultat principal (module « de dimensionnement ») est, selon le type d’essai, exprimé à 15 °C – 10 Hz (module complexe) ou 10 °C – 124 ms (traction indirecte).
Par ailleurs, les calculs à rebours à partir des mesures de déflexion en place (déflectographe ou FWD) fournissent des estimations du module en place.
Toutes ces évaluations concordent pour montrer – et quantifier – une rigidification progressive des GE. Celle-ci est rapide au début, plus lente ensuite, pour atteindre un quasi-palier après 2 ou 3 étés (figure 8). Les modules atteints lors de ce quasi-palier se situent couramment entre 3 000 et 4 000 MPa à 15 °C – 10 Hz ou 10 °C – 124 ms. Ces résultats ont été pris en compte dans la norme NF P98-12128 pour ce qui concerne les GES. Lors de l’étude d’une GES spécifique, les modules mesurés sont utilisés pour le dimensionnement de la structure correspondante.
figure_8.jpg
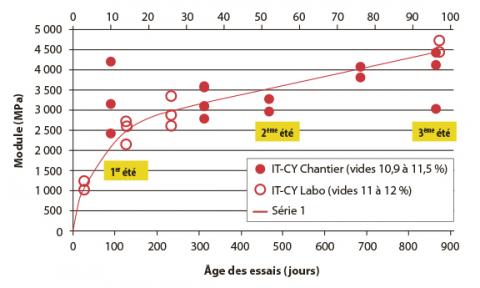
Synthèse de la méthode d’étude
Le logigramme de la méthode est présenté en figure 9. La phase préalable ne concerne a priori que les nouveaux mélanges ou ceux dans lesquels un constituant de base (granulats, émulsion) va changer. La durée du mûrissement accéléré doit être adaptée au volume de corps d’épreuve sélectionné, ainsi qu’à sa capacité d’échange avec l’atmosphère environnante, que l’on peut caractériser par le rapport entre la surface extérieure développée et le volume.
figure_9.jpg
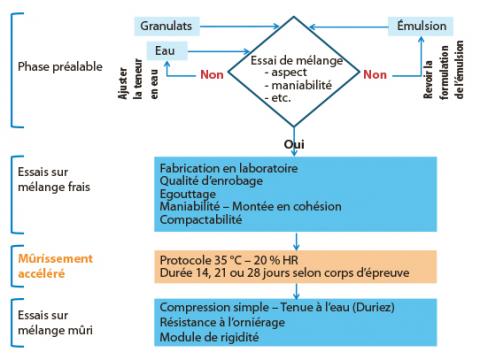
Autres propriétés
Évolution du liant
La caractérisation du liant au fil de l’évolution de la GE ne fait pas partie de la méthode d’étude proprement dite. Elle peut néanmoins présenter de l’intérêt dans le cadre de recherches, ou simplement pour l’augmentation des connaissances.
insi, à l’occasion du chantier de la RD 26 en Haute- Loire, un programme très poussé de rhéologie et d’analyses chimiques a été mené sur le liant et son évolution dans le temps. Ses résultats sont présentés dans l’article « Comportement et étude des graves-émulsion - Corrélations entre le comportement en place sur la RD 26 et le laboratoire ».
Microtexture – Perméabilités
Des recherches fondées sur des examens microscopiques, l’analyse d’image de lames minces et le calcul informatisé ont contribué à visualiser et à quantifier le pourcentage et la distribution en taille des vides. Elles ont montré, pour tous les enrobés à l’émulsion, un fort pourcentage de vides de très petite taille (« microvides »), à la différence des enrobés à chaud, qui présentent peu de micro-vides et beaucoup de « gros » vides22. Les figures 10 et 11 montrent ces différences.
figure_10.jpg

figure_11.jpg
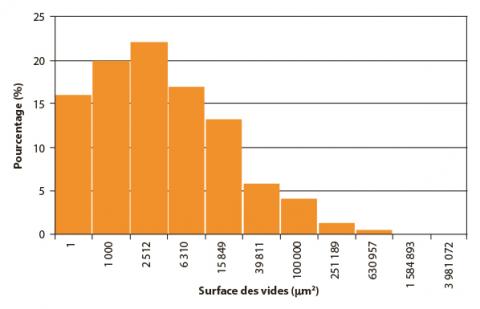
On a constaté par ailleurs que ces microvides sont majoritairement non-communicants, donc non accessibles à l’eau. Les résultats de perméabilités évoqués plus haut en sont la preuve. Les mesures de pourcentage de vides global (au banc gamma ou au nucleo-densitomètre) intègrent tous les vides, ce qui donne des chiffres élevés, dont la signification n’est pas la même que pour les enrobés à chaud. Il convient de noter que, sous trafic prolongé, les microvides disparaissent progressivement et que la microtexture d’un enrobé à l’émulsion tend, à long terme, vers celle d’un enrobé à chaud.
Tenue sous chargements répétés (fatigue)
L’observation générale du comportement des GE ne montre pas de mode de dégradation de type fissuration du bas vers le haut, caractéristique des enrobés à chaud.
Le suivi des expériences au manège de fatigue de l’Ifsttar à Nantes a mis en évidence le début de ruine des GE par décohésion progressive du bas de couche. On peut donc imaginer que le chemin de ruine sous chargements répétés est, pour un enrobé à l’émulsion, GE comprises, bien particulier. La GE a, initialement, une faible cohésion. Les chargements répétés peuvent empêcher sa cohésion de croître, voire la diminuer dans l’horizon de la couche où les contraintes sont les plus fortes. Par contraste, l’enrobé à chaud a immédiatement une forte cohésion, d’où une répartition des contraintes concentrée, pouvant conduire à une dégradation par rupture franche, fissuration évoluant vers du faïençage.
Ces constats ont conduit au lancement d’une thèse destinée à comprendre le mécanisme de dégradation des GE, à choisir un essai de laboratoire pour en rendre compte, puis à modéliser le phénomène29.
Des essais de fatigue selon le protocole de flexion 2 points ont été néanmoins réalisés, donnant des résultats difficiles à interpréter et non représentatifs du comportement en place. En effet, le sciage endommage gravement une partie des éprouvettes trapézoïdales spécifiques à cet essai, ce qui rend les résultats incertains. En tout état de cause, il est douteux que cet essai simule correctement le mode de fonctionnement de la couche de GE dans la chaussée.
Suites à donner à l’étude
Nécessité de réviser la norme NF P98-121
Les travaux menés sur les GE ont contribué à améliorer les connaissances sur ces matériaux. Ils ont aussi mis en évidence des insuffisances et des erreurs dans la version d’octobre 2014 de la norme NF P98-12128, dont la révision est devenue nécessaire.
Sans entrer dans le détail, les points à expliciter ou à corriger sont les suivants :
- définir la notion d’épaisseur nominale et de son domaine de variation ;
- limiter le pourcentage d’agrégats admissible dans les GE de reprofilage (GER) à 50 % au lieu de 100 % ;
- donner un tableau d’éléments des courbes granulométriques pour les GES ;
- moduler les teneurs en liant selon la granularité ;
- corriger le tableau de performances mécaniques (les pourcentages de vides sont identiques pour les deux modalités Duriez, ce qui est absurde : il s’agit sans doute d’une coquille d’imprimerie) ;
- corriger la spécification PCG 10 girations, impossible à respecter pour certaines GE (notamment sur la RD 26) ;
- introduire le mûrissement 35 °C – 20 % HR dans le cadre des essais Duriez, ce qui améliore la tenue à l’eau et permet de valider certaines GE qui seraient autrement rejetées ;
- demander la réalisation de l’essai à l’orniéreur pour les GES très sollicitées (trafic > T2, climat très chaud).
Dimensionnement
Jusqu’à présent, on ne dispose pas d’exemples de dégradation correspondant à la ruine in situ de GE. Il n’existe donc pas encore de critère de fatigue permettant de décider le moment où une couche de GE doit être renforcée ou remplacée. Dans ces conditions, le dimensionnement d’une GES s’appuie sur le seul critère de la déformation verticale du sol-support (ez) sur lequel la chaussée est construite. Dans cette démarche, la caractéristique retenue pour la GE est son module de rigidité.
Cette méthode de dimensionnement, incomplète au plan théorique, a toutefois été constamment confrontée aux connaissances empiriques acquises par l’observation des comportements en place. On a pu, jusqu’à maintenant, s’en satisfaire, car les GE sont restées employées sous des trafics faibles ou moyens.
L’extension de leur domaine d’emploi exige de développer une méthode plus élaborée, avec prise en compte d’une certaine fatigue (fatigue certainement différente de celle admise pour les enrobés à chaud). Il est donc nécessaire d’avancer dans l’approche théorique (modélisation) et dans l’évaluation expérimentale (définition d’un essai de laboratoire spécifique).
Besoins de recherches complémentaires
Les étapes successives de la coopération ont grandement amélioré les connaissances concernant les GE, tant sur le terrain qu’au laboratoire. Néanmoins, des questions se posent encore, qui nécessitent des recherches supplémentaires.
Comportement des enrobés avec liant fluxé
Ce thème concerne surtout les BBE, mais peut s’avérer pertinent pour certains cas particuliers de GE. Deux types de fluxants sont à envisager :
- les fluxants volatils, couramment utilisés depuis des années ;
- les fluxants réactifs, plus récents.
Les phénomènes impliqués dans le mûrissement sont bien différents entre les deux types, ainsi que les cinétiques d’évolution dans le temps. Dans les deux cas, les protocoles de mûrissement doivent être spécifiques et sont à définir pour chaque fluxant particulier. Il s’agit plus précisément de reproduire la cinétique d’évaporation des fractions légères dans le cas d’un fluxant volatil ou celle d’(auto-)polymérisation dans le cas d’un fluxant réactif.
Tenue sous chargements répétés
La thèse de Marion Lambert intitulée « Mûrissement et comportement des enrobés à l’émulsion de bitume et impact sur la réponse des chaussées sous trafic »29 constitue une avancée très intéressante. Elle pourrait être utilement poursuivie avec le recours à des essais triaxiaux.
Les étapes suivantes devraient être la détermination de critère(s) de ruine pour les GES, puis la modélisation de leurs mécanismes de dégradation et, in fine, leur méthode de dimensionnement complète. Bien entendu, cette méthode nécessitera, pour être complètement validée, d’être « calée » vis-à-vis des comportements effectivement observés sur la route.
Conclusion
La coopération présentée dans cette série d’articles, qui s’est inscrite dans la durée, est un bel exemple de ce qu’il est possible de concrétiser dès lors que les secteurs public et privé travaillent de concert. Cela ne surprendra personne, mais il est bon de rappeler que ce sont les relations entre personnes qui ont été, une fois encore, déterminantes.
Les acquis de ce travail en commun sont substantiels. L’objectif initial, qui était la mise au point de la méthodologie d’étude des GES, a été atteint, même si des améliorations ponctuelles restent nécessaires.
Les observations et mesures sur le terrain ont amené de nouvelles preuves de la bonne tenue de ces matériaux sous trafic. Ce constat global très encourageant laisse entrevoir les possibilités d’extension de leur domaine d’emploi. En parallèle, une approche performantielle des GE se dessine, avec déjà une retombée dans le domaine normatif.
La technique des GE est, on le sait, très écologique. Toutes les conditions sont donc réunies pour une accélération de son développement. Il faut maintenant espérer que tous les acteurs de la route, au premier rang desquels figurent les maîtres d’ouvrage, sauront agir dans ce sens.
RÉFÉRENCES
1. J.-P. Serfass, A. Joly, B. Mahé de la Villeglé, J. Samanos, J.-F. Corté, Y. Brosseaud, J.-P. Kerzreho, H. Odéon, « Expérimentation d’enrobés à froid au manège de fatigue », RGRA n° 734, novembre 1995, pp. 57-69.
2. D. Lesueur, J.-P. Kerzreho, Ch. Such, C. Le Roux, S. Lebec, Y, Brion, J.-C. Fabre, « Bilan de l’expérimentation Optel au manège de fatigue LCPC », RGRA n° 803, février 2002, pp. 69-76.
3. J.-P. Triquigneaux, Y. Brosseaud, « Méthodologie d’étude des graves-émulsion structurantes - Bilan de la recherche commune direction des Routes/Usirf », RGRA n° 808, juillet-août 2002, pp. 72-83.
4. J.-P. Serfass, X. Carbonneau, F. Delfosse, J.-P. Triquigneaux, « Enrobés à l’émulsion (1ère partie) - Comportement et méthodologie d’évaluation », RGRA n° 887, septembre 2010, pp 18-24.
5. J.-P. Serfass, X. Carbonneau, F. Delfosse, J -P. Triquigneaux, « Enrobés à l’émulsion (2e partie) - Comportement et évaluation de graves-émulsion », RGRA n° 889, novembre 2010, pp. 69-75.
6. J.-P. Serfass, X. Carbonneau, F. Delfosse, J.-P. Triquigneaux, « Enrobés à l’émulsion (3e partie) - Comportement et évaluation de béton bitumineux à l’émulsion », RGRA n° 890, décembre 2010, janvier 2011, pp, 36-40.
7. J.-P. Serfass, C. Leroy, L. Maison, « Enrobés à l’émulsion (4e partie) - Suites proposées aux recherches des entreprises », RGRA n° 890, décembre 2010 - janvier 2011, pp 41-42.
8. J.-P. Serfass, Ch. de la Roche, L. Wendling, V. Gaudefroy, F. Verhée, « Comportement et étude des graves-émulsion – Coopération public-privé », RGRA n° 896, septembre 2011.
9. L. Wendling, D. Guedon, V. Gaudefroy, L. Odie, J.-C. Fabre, J.-M. Balay, A. Millien, Ch. de la Roche, « Comportement et étude des graves-émulsion – Coopération public-privé – Méthodologie de préparation, d’instrumentation et de suivi de chantiers expérimentaux d’enrobés à froid à l’émulsion de bitume », RGRA n° 897, octobre 2011.
10. L. Wendling, D. Guedon, L. Odie, J.-C. Fabre, V. Gaudefroy, J. Siry, J.-M. Balay, A. Millien, Ch. de la Roche, « Comportement et étude des graves-émulsion – Coopération public-privé – Chantier expérimental de la RD 44 – Présentation du site et de son instrumentation », RGRA n° 898, novembre-décembre 2011.
11. L. Wendling, D. Guedon, L. Odie, J.-C. Fabre, V. Gaudefroy, J. Siry, J.-M. Balay, A. Millien, Ch. de la Roche, « Comportement et étude des graves-émulsion – Coopération public-privé – Chantier expérimental de la RD 44 – Suivi du comportement dans le temps », RGRA n° 899, janvier-février 2012.
12. V. Gaudefroy, J.-P. Triquigneaux, C. Petiteau, D. Claudel, F. Delfosse, M. Garbay, L. Wendling, Ch. de la Roche, « Comportement et étude des graves-émulsion – Coopération public-privé – Fabrication, prélèvement et conservation des enrobés à l’émulsion de bitume en laboratoire », RGRA n° 899, janvier-février 2012.
13. F. Delfosse, V. Gaudefroy, B. Eckmann, L. Odie, M. Garbay, F. Le Cunff, « Comportement et étude des graves-émulsion – Coopération public-privé – Caractérisation des liants bitumineux des enrobés à froid », RGRA n° 900, mars-avril 2012.
14. L. Odie, F. Delfosse, A. Beghin, Ch. Naudat, F. Le Cunff, N. Brau, « Comportement et étude des graves-émulsion – Coopération public-privé – Caractérisation de la montée en cohésion des enrobés à froid », RGRA n° 900, mars-avril 2012.
15. L. Wendling, J.-P. Triquigneaux, E. Cregut, S. Ollier, C. Petiteau, D. Claudel, L. Odie, V. Gaudefroy, « Comportement et étude des graves-émulsion – Coopération public-privé – Compactabilité des enrobés à l’émulsion de bitume », RGRA n° 901, mai 2012.
16. J-.P. Triquigneaux, L. Wendling, L. Odie, D. Claudel, V. Gaudefroy : « Comportement et étude des graves-émulsion – Coopération public-privé – Essai Duriez : teneurs en vides, performances mécaniques, sensibilité à l’eau et caractérisation des liants extraits », RGRA n° 901, mai 2012.
17. X. Carbonneau, V. Gaudefroy, F. Lubineau, S. Buisson, L. Wendling, V. Dubois, « Comportement et étude des graves-émulsion – Coopération public-privé – Résistance à l’orniérage », RGRA n° 902, juin 2012.
18. A. Beghin, L. Wendling, X. Carbonneau, Ch. de la Roche, F. Delfosse, V. Gaudefroy, L. Odie, J-M. Piau, J-P. Triquigneaux, « Comportement et étude des graves-émulsion – Coopération public-privé – Mûrissement et évolution temporelle des propriétés de l’enrobés et des caractéristiques du liant », RGRA n° 902, juin 2012.
19. Ch. de la Roche, J.-P. Serfass, « Comportement et étude des graves-émulsion – Coopération public-privé – Acquis, perspectives et suites proposées », RGRA n° 902, juin 2012.
20. NF EN 12697-19 « Mélanges bitumineux - Méthodes d’essai pour mélange hydrocarboné à chaud - Partie 19 : perméabilité des éprouvettes », septembre 2012.
21. NF P98-254-2 « Essais relatifs aux chaussées - Mesure de propriétés liées à la perméabilité des matériaux des mélanges hydrocarbonés - Partie 2 : détermination du pourcentage de vides communicants des matériaux liés », avril 1993.
22. J.-P. Serfass, « Enrobés à l’émulsion : pour une nouvelle méthode d’étude », RGRA n° 808, juillet-août 2002.
23. « Essai d’enrobage et de consistance : Procédure d’optimisation d’un mélange à l’émulsion de bitume à partir d’une appréciation visuelle et de sa consistance », Méthode d’essai LPC n° 74.
24. NF P98-257-1 « Essais relatifs aux chaussées - Homogénéité des mélanges - Partie 1 : méthode d’essai de détermination de la qualité d’enrobage manuel de matériaux hydrocarbonés à froid », août 2004.
25. « Mesure du taux d’égouttage d’un enrobé à l’émulsion de bitume », Projet de méthode d’essai LPC n° 75.
26. « Mesure de la montée en cohésion d’un enrobé à l’émulsion de bitume : essai de maniabilité, essai de mesure de couple », Projet de méthode d’essai LPC n° 76.
27. NF EN 12697-26 « Mélanges bitumineux - Méthodes d’essai pour mélange hydrocarboné à chaud - Partie 26 : module de rigidité », juin 2012.
28. NF P98-121 « Assises de chaussées - Grave-émulsion - Définition - Classification - Caractéristiques - Fabrication - Mise en oeuvre », octobre 2014.
29. Marion Lambert, « Mûrissement et comportement des enrobés bitumineux à l’émulsion de bitume et impact sur la réponse des chaussées sous trafic », thèse en préparation à l’université de Limoges.