L’industrie cimentière française fait face à de nombreux défis technologiques et s’inscrit depuis des années dans une stratégie de décarbonation et de valorisation des déchets anthropiques à grande échelle. Acteurs incontournables de l’aménagement, le béton et son constituant principal, le ciment, qui allient performances techniques, esthétiques et économiques, sont en pleine mutation pour répondre aux enjeux climatiques.
Le béton et son principal composant, le ciment, sont des matériaux essentiels, au cœur de l’acte de construire, notamment pour tout ce qui concerne les aménagements routiers et les infrastructures de transport.
L’industrie cimentière, soucieuse de son impact environnemental, travaille depuis des dizaines d’années à améliorer son process et ses produits. Ainsi, les industriels n’ont de cesse de faire évoluer le ciment afin de réduire son empreinte carbone et de valoriser des déchets anthropiques, en particulier pour ce qui concerne les combustibles utilisés lors de sa fabrication et les matériaux de substitution au clinker, principe actif des liants hydrauliques.
Pour aller encore plus loin, l’industrie cimentière française a publié sa feuille de route de décarbonation, qui prévoit une baisse de ses émissions de 24 % en 2030 et de 80 % en 2050 par rapport à 2015. L’enjeu est de taille, car le béton et, plus largement, les matériaux cimentaires, incontournables pour le secteur du bâtiment et des travaux publics, doivent continuer de s’inscrire dans une démarche de développement durable et responsable.
Le béton, allié de choix de la construction routière
Le béton est un matériau largement répandu dans le monde de la construction, et la route n’y déroge pas. Que ce soit pour la réalisation de fondations, revêtements routiers, plates-formes, ouvrages de protection (glissières de sécurité, caniveaux coulés en place…), aménagements décoratifs, produits modulaires (pavés ou bordures), ou d’autres solutions spécifiques comme les bétons de calage et les coulis autocompactants…, on estime la part des bétons utilisés dans la route à environ 15 % des bétons fabriqués en centrale en France, soit l’équivalent de 6 millions de m3.
Plusieurs facteurs expliquent ce développement :
- Le béton est un matériau facile d’utilisation, performant, durable et économiquement intéressant.
- Il est produit localement (distance moyenne de livraison entre une centrale à béton et un chantier : 15 à 20 km).
- Il permet de répondre aux exigences les plus sévères : giratoires utilisés par des poids lourds, péages, aéroports, plates-formes de transports collectifs en site propre (TCSP), plates-formes industrielles, arrêts de bus…
- Il peut être retenu pour ses qualités esthétiques (nombreuses teintes et finitions possibles) et de clarté (albédo élevé).
Béton, ciment et CO2
Il n’est pas encore possible de produire du béton sans impact carbone. Le béton représente en France moins de 2 % des émissions de CO2 (environ 7 % à l’échelle mondiale), émissions qui sont dues, en grande partie, au composé principal et principe actif du ciment : le clinker. Les émissions de CO2 lors du process de fabrication du ciment sont pour 1/3 liées à l’utilisation des combustibles lors de la cuisson du calcaire et de l’argile à haute température et pour les 2/3 restant à la décarbonatation du calcaire lors de la cuisson (CaCO3 => CaO + CO2).
Réduire l’impact carbone
Depuis de nombreuses années, l’industrie cimentière investit dans la décarbonation de son activité, notamment grâce à l’utilisation de combustibles de substitution, mais également en réduisant le pourcentage de clinker dans les ciments au profit de matériaux alternatifs moins « carbonés » et « activables » par le clinker. Elle travaille avec l’ensemble de la filière béton pour le développement de nouvelles formulations et l’optimisation des quantités de ciment par mètre cube de béton.
Les émissions de l’industrie cimentière ont ainsi diminué de près de 40 % entre 1990 et 2019 (figure 1).
figure_1.png
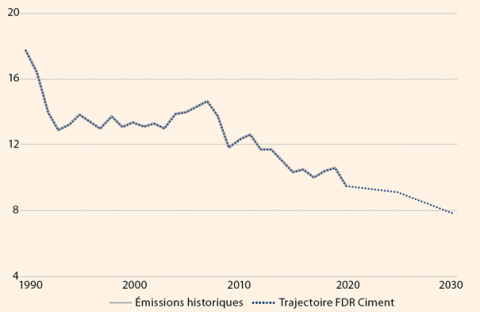
Dans un contexte de prise de conscience croissante de la nécessité de réduire les impacts environnementaux, l’industrie cimentière s’est fixée une feuille de route de décarbonation avec une baisse de 24 % en 2030 et de 80 % en 2050 par rapport à 2015. Pour atteindre un niveau d’émissions de l’ordre de 2 Mt de CO2 à cet horizon, les leviers sont clairement identifiés.
Les efforts portent d’abord sur les moyens industriels de production :
- l’efficacité énergétique des sites de production, avec la modernisation de l’outil industriel (nouveaux fours, pré-calcinateur…) ;
- le remplacement toujours plus important des combustibles fossiles par des combustibles alternatifs (déchets de biomasse, emballages, déchets industriels dangereux...) avec un objectif de 80 % de substitution des combustibles fossiles en 2030 (contre 44 % actuellement) ;
- la mise sur le marché de nouveaux ciments bas carbone.
Par ailleurs, pour atteindre les hauts niveaux de performances attendus en 2050, le déploiement de technologies de rupture doit être préparé. L’une des voies les plus prometteuses concerne le captage, le stockage et l’utilisation du CO2 émis à la source par les cimenteries (technologies CCUS : Carbon Capture, Use and Storage).
La concentration de CO2 à la sortie des cheminées d’une cimenterie est actuellement de l’ordre de 20 %. Plusieurs systèmes pour le concentrer et le récupérer sont en test en Europe, avec le soutien de fonds européens et des pouvoirs publics. Le développement de ces technologies est un chantier complexe, qui nécessite de recourir à des infrastructures de compression, de stockage et d’acheminement pour conserver durablement le carbone et pour pouvoir le réutiliser. Ces solutions impliquent donc des investissements lourds et des mesures d’accompagnement.
En parallèle, la quête de solutions bas carbone innovantes se poursuit, notamment en France, avec une R&D active sur des travaux concernant notamment :
- l’optimisation des activateurs de prise du béton ;
- la carbonatation accélérée des granulats de béton recyclé, granulats qui deviennent « carbonégatifs » (projet national FastCarb).
Reconcevoir le matériau béton
La réduction significative de l’impact environnemental du béton passe également par une reconception de sa formulation.
Le liant
La réduction de la part du clinker dans le ciment est déjà une réalité et deux nouvelles normes européennes, NF EN 197-51 et NF EN 197-62, compléteront cette offre de ciments bas carbone :
- La norme NF EN 197-5 entérine l’arrivée de ciments nouveaux, dits ternaires, où le clinker est associé à d’autres composants déjà connus, comme le laitier de haut fourneau, les cendres volantes, les pouzzolanes naturelles calcinées ou le calcaire.
- Quant à la norme NF EN 197-6, elle introduit pour la première fois depuis 1994 un composant nouveau – les fines de béton recyclées –, dont les études ont montré qu’elles ont un comportement similaire aux fines de calcaires et font entrer le ciment dans l’économie circulaire en le recyclant en boucle fermé.
L’offre cimentaire se décline donc aujourd’hui non seulement techniquement, mais également en termes d’empreinte carbone (figure 2).
figure_2.png
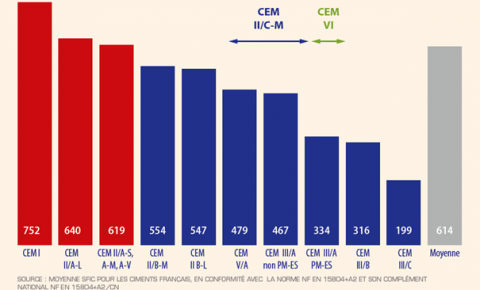
L’utilisation courante de ces différents ciments ayant une empreinte carbone plus faible s’accroît progressivement grâce aux travaux menés :
- Sur les performances, à jeune âge notamment. Les résistances obtenues sont bien inférieures à celles des ciments majoritairement composés de clinker. Les industriels de la filière, et notamment les services R&D des producteurs d’adjuvants, cherchent à proposer des solutions d’accélération toujours plus performantes et spécifiques pour ces nouveaux ciments.
- Sur l’identification et la normalisation de nouveaux substituts au clinker, comme les argiles calcinées, les fines de béton recyclées, afin de favoriser leur utilisation dans un contexte très réglementé, pour assurer qualité et pérennité des ouvrages. Ces travaux peuvent également ouvrir de nouveaux champs face à la disponibilité limitée des constituants alternatifs décarbonés que sont les laitiers de haut fourneau et les cendres volantes.
Le dosage
Pour réduire l’empreinte carbone du béton, une autre voie à suivre est l’optimisation du dosage en liant. La plupart des bétons formulés aujourd’hui atteignent les seuils minimum de dosage en ciment spécifiés dans la réglementation. Il est alors envisageable de se poser la question de la réduction de ces dosages imposés pour certaines applications peu sollicitées ou destinées à un usage provisoire.
Côté routier, l’utilisation de moyens de mise en œuvre spécifiques, comme les compacteurs et les cylindres vibrants, sont des atouts pour optimiser l’efficacité du liant introduit dans le matériau : avec les bétons compactés routiers (BCR), on peut atteindre des performances mécaniques équivalentes, voire supérieures, aux bétons coulés en place, malgré un dosage en liant significativement réduit, et donc un bilan carbone bien amélioré.
Le recyclage et la valorisation de coproduits d’origine naturelle
La question environnementale ne se résume pas au seul impact CO2. La préservation des ressources naturelles, la valorisation des matériaux alternatifs et le développement du recyclage sont également des défis à relever.
Le secteur routier applique déjà depuis de nombreuses années les principes de l’économie circulaire en valorisant des matériaux au lieu de les enfouir ou de les incinérer. Les granulats de béton recyclé, par exemple, permettent d’utiliser les bétons issus de la déconstruction (environ 20 millions de tonnes disponibles aujourd’hui). Les travaux menés au cours des dernières années ont contribué à préciser les taux de substitution des granulats recyclés tout en conservant le même niveau d’exigence sur les ouvrages (projet national Recybéton3).
Il est également possible de substituer aux granulats traditionnels des granulats agrosourcés (exemple du bois dans les murs anti-bruit) ou des fibres végétales (chanvre…), pour certains produits de voirie drainants, des coquilles d’huîtres ou de pétoncles...
Privilégier la durabilité
Un des grands avantages du béton par rapport aux autres matériaux, c’est sa durabilité. Cela est d’autant plus vrai lorsque l’ouvrage est soumis à de fortes contraintes de fonctionnement : giratoire sollicité par des poids lourds, péages, arrêts de bus, aéroports, plates-formes industrielles…
L’intérêt est également indiscutable pour les zones où le trafic est difficile à reporter pour des entretiens : boulevards périphériques, accès aux métropoles, carrefours importants, gares…
Sur des ouvrages « moyens », le béton est une solution économique et environnementale à privilégier, dès lors que sont prises en compte des durées de vie supérieures à 20 ans. De plus, les propriétés intrinsèques du béton et son mode de fonctionnement dans la route (travail en flexion) en font le meilleur allié pour les conceptions de longue durée de vie et les ouvrages fortement sollicités.
Pour confirmer cet avantage, on peut citer de nombreux exemples d’ouvrages réalisés en béton qui détiennent des records (longévité sans travaux de réparation, bilan économique, bilan environnemental) : autoroute A6 (construite dans les années 1960 pour une durée de 20 ans, qui assure toujours sa fonction structurelle, recouverte par des couches bitumineuses), RN 141 (section de Rassats-Favrauds, chaussée composite en BAC sur GB avec un BBTM en surface construite en 1998, qui n’a nécessité aucun entretien en 25 années de service sous trafic T0+), giratoires (pour lesquels la solution béton s’impose face aux agressions du trafic PL)...
Conclusion
Cet article devrait répondre à certaines interrogations des maîtres d’ouvrage et/ou maîtres d’œuvre et les rassurer quant à l’avenir d’un matériau particulièrement bien adapté aux besoins et pourtant souvent invisible dans les infrastructures routières.
Le béton, matériau local présentant de nombreux avantages, est aussi un matériau vivant qui évolue constamment pour répondre aux besoins quotidiens. De plus, tous les acteurs de l’industrie cimentière travaillent à la réduction de son empreinte carbone pour le rendre plus vertueux.
Il convient donc de souhaiter aux routes une longue vie en compagnie du béton.
Références
- NF EN 197-5, « Ciment - Partie 5 : Ciment Portland composé CEM II/C-M et Ciment composé CEM VI », mai 2021.
- NF EN 197-6, « Ciment - Partie 6 : Ciment à base de matériaux de construction recyclés », publication prévue en 2023.
- J. Roudier, H. Colina, F. de Larrard, « Projet national Recybéton – Synthèse des recommandations », RGRA n° 959, novembre-décembre 2018.