Le taux de recyclage annuel réalisé dans les enrobés à chaud et les enrobés tièdes en France poursuit tranquillement sa progression au fil des années. Malgré un taux annuel passé de 12,5 % en 2013 à 16,3 % en 2018, la France reste encore en retard par rapport à d’autres pays d’Europe tel que l’Autriche, le Danemark, la Finlande, l’Allemagne et la Belgique, qui affichent des taux de recyclage annuels en 2018 compris entre 17,7 % et 29,1 % (source : EAPA 2018). Néanmoins, si elle n’est pas dans les premiers de la classe, elle demeure loin des derniers. En effet, de nombreux autres pays d’Europe restent encore aujourd’hui en dessous d’un taux de recyclage annuel de 10 %.
Parmi les raisons qui expliquent le taux de recyclage annuel français, qualifiable de moyen (figure 1), figurent les nombreuses ressources disponibles : la France n’ayant pas de problème d’approvisionnement en granulats aussi bien en termes de quantité que de qualité, elle n’a pas eu la nécessité de recourir au recyclage. Par ailleurs, une certaine reticence des donneurs d’ordre pour promouvoir les enrobés recyclés a limité la progression des taux de recyclage. Enfin, les installations ne pouvaient pas toutes produire des enrobés recyclés à fort taux (30 à 50 %), voire à très forts taux (50 à 70 %), point indispensable pour atteindre des taux annuels de recyclage élevés.
figure_1.jpg
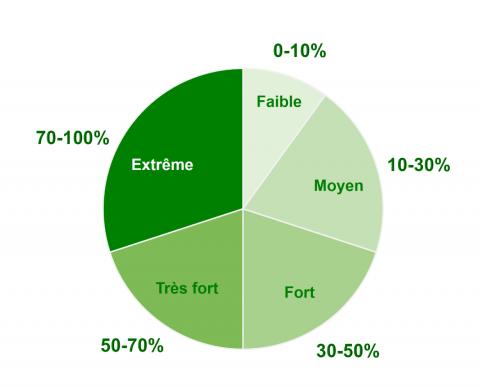
Au cours des dernières années, on a pu assister à une véritable prise de conscience de l’ensemble des acteurs de la route pour la promotion de l’augmentation des taux de recyclage dans les enrobés routiers, ce qui devrait donner l’opportunité à la France de se positionner à court ou moyen terme parmi les premiers de la classe.
Le recyclage est une nécessité dans tous les domaines, et tout particulièrement pour les enrobés routiers, qui offrent l’avantage d’être 100 % recyclables.
En tant que constructeur d’usines d’enrobés, Marini-Ermont, précurseur dans les usines permettant de recycler les agrégats d’enrobés (AE) de manière industrielle dans les années 1980, a développé, au début des années 1990, des usines pouvant recycler régulièrement jusqu’à 50 % d’AE avec la technique brevetée Retroflux. Cette technologie, qui a fait ses preuves dans un premier temps dans les pays d’Europe du Nord, pionniers en terme de recyclage, demeure aujourd’hui une solution idéale pour le recyclage des AE à fort taux, en protégeant l’environnement et en garantissant la qualité des enrobés produits à travers notamment la remobilisation totale du liant.
À titre d’information, certaines usines françaises équipées de cette technologie affichent un taux de recyclage annuel avoisinant les 30 %, ce qui montre qu’il est possible d’atteindre des taux élevés sans forcement avoir recours aux installations très forts taux.
MAÎTRISE DE LA QUALITÉ DES ENROBÉS À FORT TAUX DE RECYCLAGE
Dans le cadre du projet national Multirecyclage des enrobés (PN Mure)1, l’ensemble des chantiers ont été réalisés avec des enrobés en provenance de 6 usines d’origines différentes, parmi lesquelles 4 étaient équipées de la technologie Retroflux Marini-Ermont (photo 1). L’ensemble des résultats d’analyse réalisés sur ces 4 usines confirme la qualité des enrobés produits et une remobilisation totale du liant dans ces derniers.
photo_1.jpg
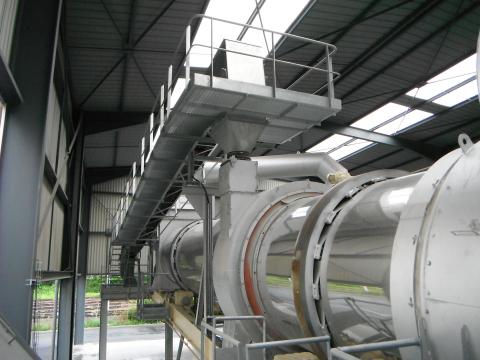
Ces résulats ne sont pas le fruit du hasard. En effet, le process de recyclage joue un rôle clé dans la qualité des enrobés produits, la remobilisation totale du liant reposant sur 3 facteurs essentiel du process :
- La préservation du bitume des AE lors du procédé de séchage et de chauffage, en évitant tout contact des AE avec le rayonnement d’une flamme, des gaz à très haute température ou des matériaux à très haute température.
- Le mélange très long des AE avec les granulats afin de faire migrer le liant des AE vers les granulats, jusqu’à atteindre un mélange homogène.
- La protection du liant d’apport injecté sur un mélange à la température homogène (celle de l’enrobé) et malaxé pendant une longue durée afin d’assurer l’étape finale de la remobilisation du liant. Les chantiers réalisés à fort taux de recyclage dans le cadre du projet Mure ont montré que les forts taux de recyclage (30 à 50 %) sont parfaitement maîtrisés par les grands acteurs routiers français, membres du PN Mure.
USINE TRX 100 % : UNE COLLABORATION ENTRE MARINI-ERMONT ET EUROVIA
En 2018, en parallèle du projet Mure, le constructeur Marini-Ermont, convaincu de l’intérêt de développer des usines très forts taux de recyclage écologiques, a répondu favorablement à la demande de la société Eurovia pour l’accompagner dans le projet « La route 100 % recyclée », lauréat de l’appel à projets « Route du futur » opéré par l’Ademe. C’est dans ce contexte qu’il a développé l’usine d’enrobés hypermobile TRX 100 %, qui permet de recycler de 0 à 100 % d’AE tout en garantissant la qualité des enrobés recyclés et en préservant l’environnement2.
Cette usine polyvalente, fondée sur une nouvelle technologie brevetée, reprend les 3 facteurs essentiels cités précédement pour garantir la qualité des enrobés recyclés, et ce, sur toute la plage de recyclage de l’installation.
Cette usine a déjà produit les enrobés pour de nombreux chantiers vitrines à très forts taux et taux extrêmes tels que :
- 1 km d’autoroute réalisé avec des enrobés 100 % recyclés sur l’A10 entre Bordeaux et Paris pour le compte de Vinci Autoroutes3 ;
- plusieurs kilomètres réalisés avec des enrobés à 70 % d’AE sur l’A10 pour le compte de Vinci Autoroutes et sur différentes portions de routes des départements de la Charente, la Charente-Maritime et la Vienne pour le compte de l’État. À nouveau, ces différents chantiers confirment que les enrobés recyclés à très fort taux ne sont plus du domaine du rêve, mais bien une réalité parfaitement maîtrisée par certains grands acteurs de la route, rendue possible grâce au développement de nouveaux procédés de recyclage innovants.
USINE TSX, POUR FACILITER LES TRÈS FORTS TAUX DE RECYCLAGE
Marini-Ermont a décidé de pousuivre ses développements pour pouvoir augmenter la production des très forts taux de recyclage sans pour autant viser les taux extrêmes.
Une nouvelle technologie, baptisée TSX, vient d’être brevetée et développée par Marini-Ermont afin de mettre sur le marché une nouvelle gamme d’usines d’enrobés polyvantes, hypermobiles ou fixes, permettant de produire de manière simple et économique des enrobés recyclés avec des taux de recyclage de 0 à 70 % tout en garantissant la qualité des enrobés recyclés et en préservant l’environnement.
Cette technologie est fondée sur un tambour sécheur à courant parallèle comportant 3 zones distinctes monté en série avec un malaxeur à double arbres synchronisés (figure 2) :
- La première zone du tambour, appelée zone de combustion, est celle dans laquelle se développe la flamme du brûleur qui génère des gaz chauds pour sécher et chauffer les matériaux (granulats et AE).
- Dans une deuxième zone du tambour, les gaz chauds issus de la première zone vont échanger dans un premier temps avec les granulats seuls afin de les sécher et de les chauffer, de stocker de l’énergie dans les granulats et d’abaisser les températures de gaz. Cette zone assure aussi le rôle de bouclier thermique pour éviter tout rayonnement de flamme sur la troisième zone.
- Dans la troisième et dernière zone du tambour, les AE, introduits dans le tambour via un anneau de recyclage, sont séchés grâce au procédé d’échange thermique DuoTherm, qui combine un échange thermique entre les AE et, d’une part, les granulats légèrement surchauffés et, d’autre part, les gaz à température modérée ayant préalablement échangé avec les granulats. Durant la traversée de toute cette zone très longue, le liant des AE migre de manière homogène sur l’ensemble des granulats afin de réaliser la première phase de remobilisation du liant.
figure_2.jpg
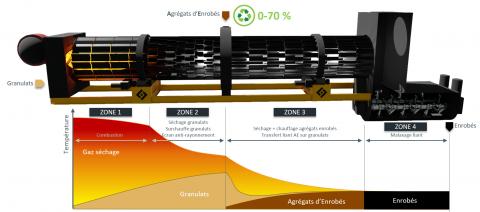
En sortie de tambour, le mélange homogène en granulométrie et en température est acheminé dans le malaxeur à double arbres synchronisés, où il est malaxé avec le liant d’apport et un éventuel régénérant. Un temps de malaxage très long garantit la seconde phase d’achèvement de la remobilisation du liant.
Cette nouvelle technologie brevetée permet ainsi de produire des enrobés de qualité tout en préservant l’environnement, en n’exposant jamais le liant des AE à la radiation d’une flamme ou à de fortes températures tout au long du process de chauffage et de malaxage des AE.
La technologie TSX devient la seule technologie au monde à même de recycler simplement jusqu’à 70 % d’AE sans compromis sur la qualité des enrobés et sur l’environnement avec un seul tambour et un seul brûleur. Cette technologie fondée sur le process d’échange thermique DuoTherm allie polyvalence et simplicité d’utilisation. Elle peut faire varier le taux de recyclage à la demande en fonction des besoins des formulations sans aucune adaptation spécifique sur l’installation.
Les premiers enrobés produits avec la technologie TSX verront le jour sur le réseau routier français dans le courant de l’année 2021.
RÉFÉRENCES
- Dossier « Bilan des projets Mure et ImprovMure », RGRA n° 968, novembre 2019.
- T. de Sars, « TRX 100 % de Marini-Ermont : le recyclage n’a plus de limite », RGRA n° 963, mai 2019.
- Y. Marquet, O. Petry, J.-A. Decamps, N. Paquet, « La route 100 % recyclée », RGRA n° 963, mai 2019.